DigiFacture Modular
Production Management System
Centralized factory machine data management
for improved production efficiency.
Industry Challenges
Three common issues in factory production processes
-
Uneven production task allocation
leading to low efficiencyTraditional factories often rely on the experience of production management personnel for task allocation.
It's typically based on the production units within the factory.
However, when equipment malfunctions or urgent tasks arise, this often leads to imbalances in production capacity at different workstations and uneven task allocation, resulting in reduced production efficiency. -
Inability to track production status
in real-time leading to delayThe production efficiency and equipment utilization rates at each workstation are manually recorded by employees on a per-shift or daily basis.
Due to the inability to monitor production status in real-time, often leads to discrepancies between planned and actual production output.
This results in order delays and excess inventory issues.
-
Uneven production task allocation
leading to low efficiencyVarious factors such as machine conditions, material availability, and labor issues can impact the production process.
Due to the inability to track and address them in a timely manner, these can lead to machine idleness and labor underutilization, resulting in inefficient working hours and increased production costs.
DigiFacture One-Stop Production Data Management
for Real-Time Resolution of Production Line Issues
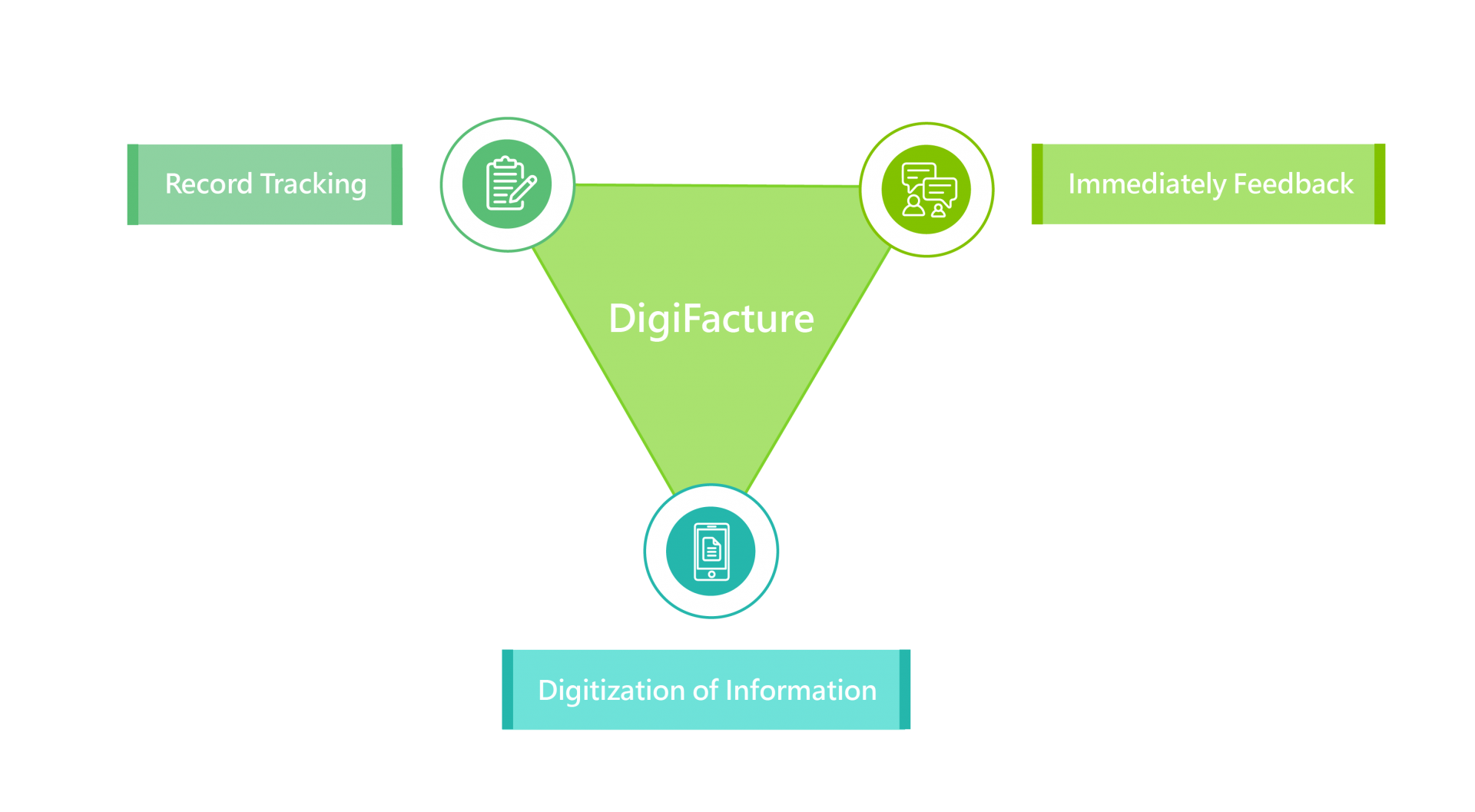
Digitizing Production Data for Instant Resolution
of Machine Abnormalities and Downtime
The factory improves Overall Equipment Efficiency (OEE),
the key is to identify the causes of downtime from relevant data when the machinery is not functioning properly.
With DigiFacture's assistance, the factory can efficiently manage production efficiency and yield across the three major processes.
Optimizing Production Management Across Three Processes
-
Digitization of Information
• Workstation Process & Equipment Management
Segmented by factory production units, establishing digital information for equipment, workstations and processes within the system.
• Order Generation and Maintenance Management
Constructing production task information for equipment, workstations, and other production units within the system.
• Order and Equipment Report
Utilizing the system's condition feedback mechanism to document condition events within the system. -
Record Tracking
• Order Generation and Maintenance Management
Production tracking and alerting for each production unit.
• Order and Equipment Report
Tracking and alerting of condition events for each production unit.
-
Immediately Feedback
• Order and Equipment ReportBarcode reporting mechanism for real-time synchronization of production information.
Five Production Management Application Modules
-
Equipment registration, maintenance, and category configuration
-
Workstation category setup, addition, and maintenance; process addition and maintenance
-
Material item setup and addition, as well as maintenance of item composition configuration and item routing setup
-
Barcode reporting mechanism, real-time synchronization of production information, and condition data between pre-production and post-production units, as well as management units.
-
User permission management and system task scheduling configuration
Application Benefits
-
Increasing production efficiency and reducing non-productive hours
1. Distribution of production tasks based on reference work data, combining real-time task tracking capabilities, reducing production line idle time and preventing task overload for personnel.
2. Barcode reporting mechanism to enhance reporting timeliness. Reducing administrative work time and the error rate in manual labor. -
Reducing rework costs
1. Synchronizing information between the pre-production and post-production units, improving the accuracy of production data. Enhancing transparency in on-site production capacity and progress, preventing production line downtime due to defective products.
2. Improving real-time control of work-in-progress quantities to avoid wasting production resources.
-
Automation of report generation
1. After inputting work reporting information, the system can automatically generate relevant reports. Reducing the time and cost of personnel in repetitive tasks while avoiding human errors in manual operations.
2. Real-time updating of reports, providing current production status information for future process optimization and adjustment benefits. -
Production management visualization
1. Visualized charts help on-site managers monitor production status, make decisions, analyze, and adjust the production facility.
2.Providing remote managers with real-time visual charts for achieving continuous production line monitoring and systematic management, enhancing the efficiency of remote management.
DigiFacture Modular
Production Management System
Implementing DigiFacture,
the modular production management system
Significantly improving production efficiency